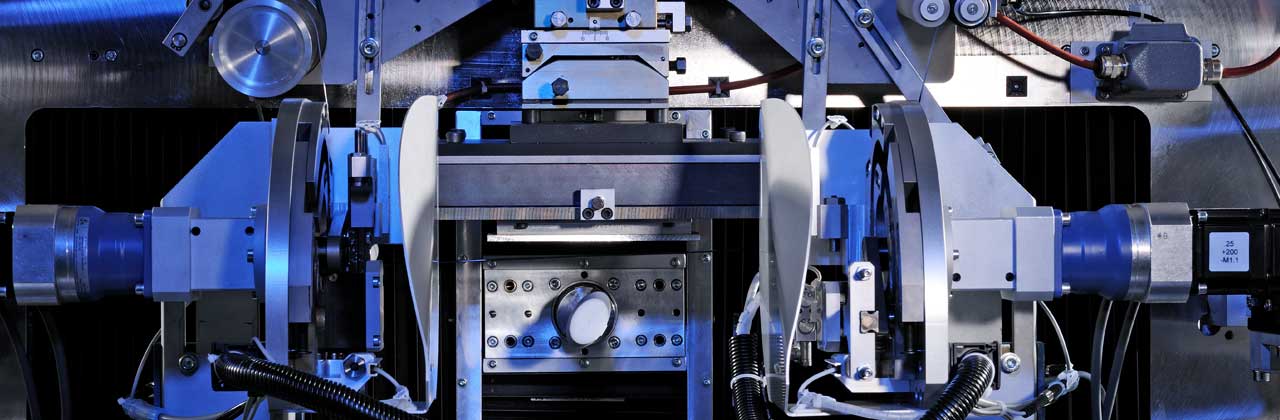
Processes
Stamping technology from KURZ
The most efficient route to unlimited design variety
One Mold – Multiple Processes
Sometimes the most efficient way of decorating your components is what determines your competitive advantage. This is why it is important for us at KURZ to provide a dynamic, innovative range of technologies that can be flexible and adapt to meet your requirements. We are the only company in the world that can offer all decorating processes from a single source.
Whether you require traditional plastic injection molding, in-mold decorating (IMD), insert molding, in-mold labeling (IML) or hot stamping, various processes can be carried out with just one tool, allowing you to choose the most favorable decorating process.
IPD-Skin
New decoration technology
Benefits:
- Maximum design flexibility for small to series production and special editions
- Decoration process can be used for small to large size parts
- Various decoration substrates with economic haptic and optical effects
- Low temperature and pressure load result in better tactile finishes
- High flexibility and fast changeover between different decoration parts and patterns
Vertical Stamping
Process advantages:
Vertical stamping offers a simple means of decorating two-dimensional plastic surfaces. It can accommodate ...
- Decoration of the full surface or part of the surface
- Numerous variations to satisfy different part requirements
- First and second surface decoration
- Same process can be used for hot stamping foils or heat transfer single images
Unlimited design options with KURZ standard foils for interior and exterior use
- Metallic surfaces, aluminium and chrome
- Unicolor
- Brushed and metallic effect
- Pigmented colors
- Metallic and pigmented patterns
- Holographic effects
- Wood design
- Heat Transfer
- Digital Heat Transfer
Environmentally friendly decoration process
- No wet varnishes, inks or solivents used in the production process
- Expensive surface appearance like chrome or metallic effects using a dry process
- Safe for your employees and manufacturing process
Roll-on Stamping
Process advantages:
Process advantages:Roll-on stamping offers a simple means of decorating two-dimensional plastic surfaces. It can accomodate...
- Full surface or partial decoration
- Numerous variations for different decoration requirements
- First and second surface decoration
- Same process can be used for hot stamping foils or heat transfer single images
KURZ has virtually unlimited design options for interior and exterior use of its standard foils.
These designs include ...
- Metallic finishes such as aluminum and chrome
- Unicolor
- Brushed and metallic effects
- Wood designs
The decoration process is environmentally friendly ...
- No wet varnishes are used in production
- Finishes that resemble expensive chromes or metallics can now be created from a dry process
3DHS® - the Innovation:
- Hot stamping is now three-dimensional
- Economical decoration method
- Foil, tooling, and machine as a complete solution package - perfectly aligned for seamless implementation
As the global leader in hot stamping technology, we continue to develop new solutions and innovative decoration methods that are versatile and economically efficient.
Today we have expand our wide-range of services in hot stamping with a new patented process: 3DHS®.
3DHS® stands for 3D hot stamping. For the first time ever, hot stamping is possible on 3D geometries that historically have been impossible to decorate with traditional stamping methods. Defects such as wrinkling, decoration misses, and poor adhesion could all be related to improper part tooling, part geometry, machine capabilities, and/or a combination of all three. Today, KURZ has the solution resolve and avoid these issues with 3DHS®.
With the 3DHS® process, plastic parts, for example, a one-piece cover, are provided with a decorative layer - in our example, real chrome foil/coating. This dry and solvent-free process helps you avoid the unnecessary labor and equipment cost that come with spraying, plating, galvanizing, or painting.
Other 3DHS® advantages include an environmentally friendly process that doesn't require all the harsh manufacturing processes, chemicals, and application steps that can be hazardous for your employees and increases your carbon footprint. Our system is flexible and robust to assist you in design changes by simply changing out the roll of foil and putting a new color or pattern on the machine.
In-Mold Decoration (IMD)
The IMD-technique combines molding and hot stamping into one working operation.
This provides complete decoration of plastic parts during the molding operation, the production costs can be reduced considerably: post molding decoration, in-process inventory and additional working steps can be eliminated.
This process is working with a modified hot stamping foil which is being fed through the mold by a foil feeding unit. After closing the mold, the foil is pressed into the cavity by the injection molding material.
The injection temperature and molding pressure transfer the decorative layer from a polyester carrier and marry it with the plastic part. This decoration method provides an extremely high end looking part and the topcoats have been engineered to pass simple to extremely difficult testing specifications. Making IMD a fit for almost any application and industry.
Insert Molding
As an addition to the IMD-decoration, Insert Molding is often used when a higher deformation or forming of the foil is required.
Insert Molding combines hot stamping process, vacuum-forming and molding process into one simple process delivering superior part decoration able to pass the toughest specifications in the industry.
KURZ is happy to assist you in determining the best decoration technology for your aesthetic and functional requirements.
IMD IML Decoration
This technology simultaneously applies the transparent, conductive PolyTC foil for touch sensor and decorative coatings on components during the injection molding process. The process combines in-mold labeling (IML) and in-mold decoration (IMD):
The PolyTC label is inserted in on the core side of the mold. The IMD decorating foil is positioned on the opposite side. After the injection molding process the finished part can be removed and installed.
Typical areas of application include control panels in the automotive or home appliance sector, multi-touch sensors in mobile communications, and innovative capacitive controls in consumer electronic applications.
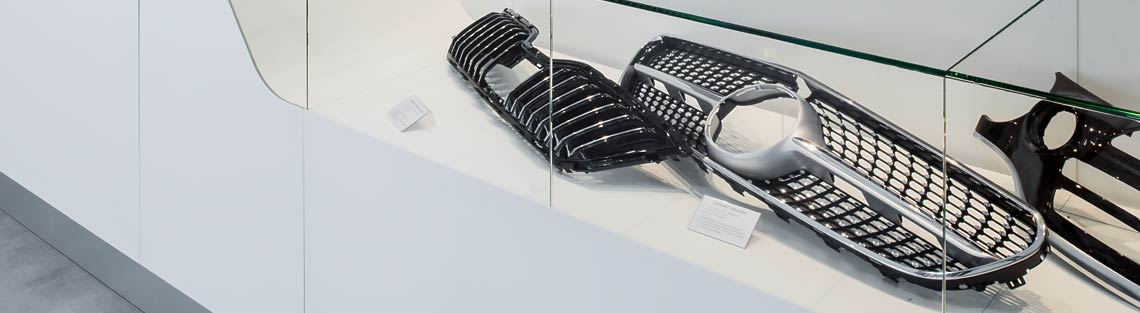